Flex4Green
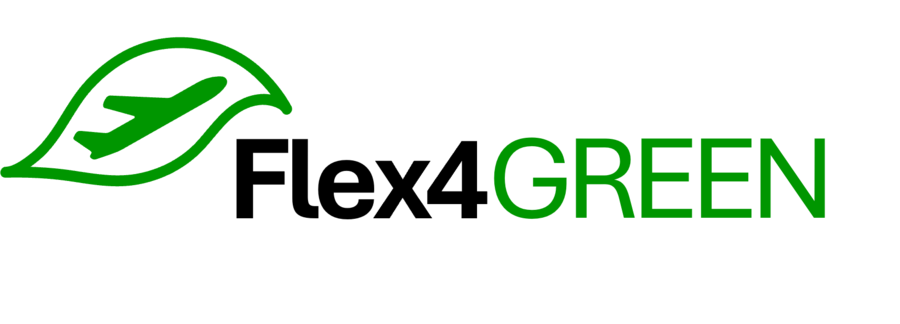
Assembly processes in the aircraft industry are characterized by many high-precision individual parts that are assembled under the strictest process conditions. Process sequences and defined time windows must be adhered to precisely. Under these conditions, even the smallest unavoidable disturbances in the process sequences mean that extensive changes have to be made to the work plan.
One example occurs during the bonding of components to partial shells of the fuselage. After the robot-assisted application of the adhesive, the components must be positioned by the same robot within a certain time window. Applying the adhesive and positioning a component alternately for individual parts is uneconomical. Applying the adhesive to several components is more efficient. However, if the upper time limit between adhesive application and positioning is exceeded, the adhesive must be laboriously removed manually before the process can be resumed. In this process, process planning and the reaction to necessary changes in the workflow under disruptive influences have a major impact on sustainable production, both economically and ecologically.
The Flex4Green project aims to automate work planning and use artificial intelligence to optimize resource consumption, thereby making a decisive contribution to increasing sustainability in the aviation industry.
The research and development of the AI systems is taking place at two AIRBUS Group sites in Germany. In Augsburg, the processes for the partial assembly of aircraft shells in multifunctional cells are being optimized, while in Nordenham, work planning for section assembly is being designed with the cooperation of humans and robots.
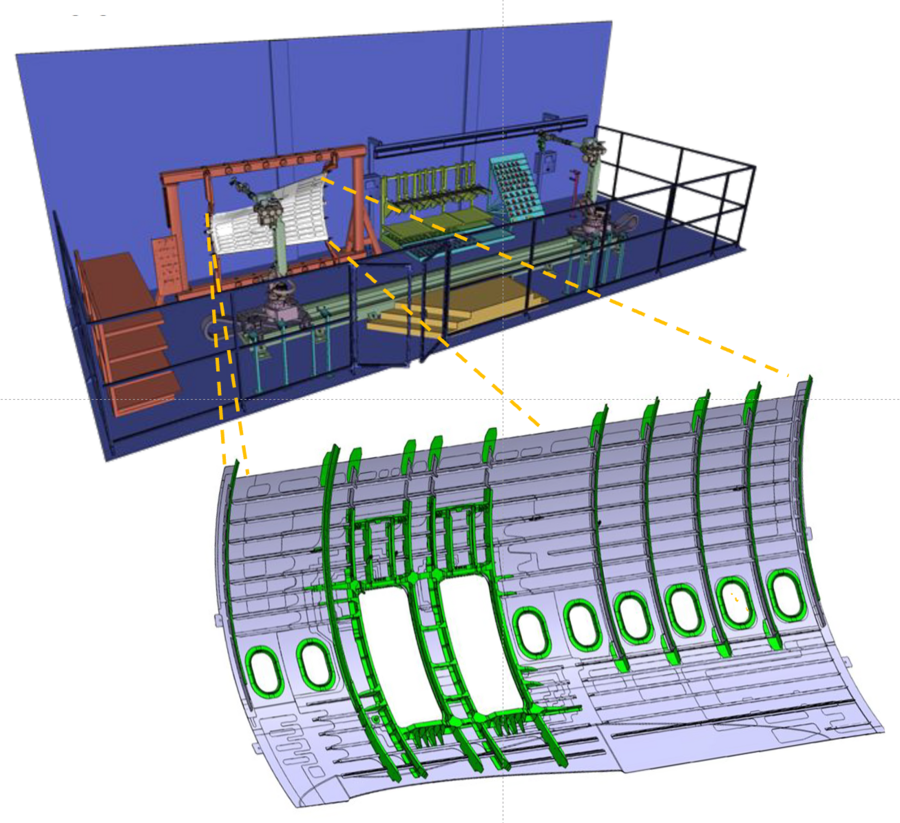